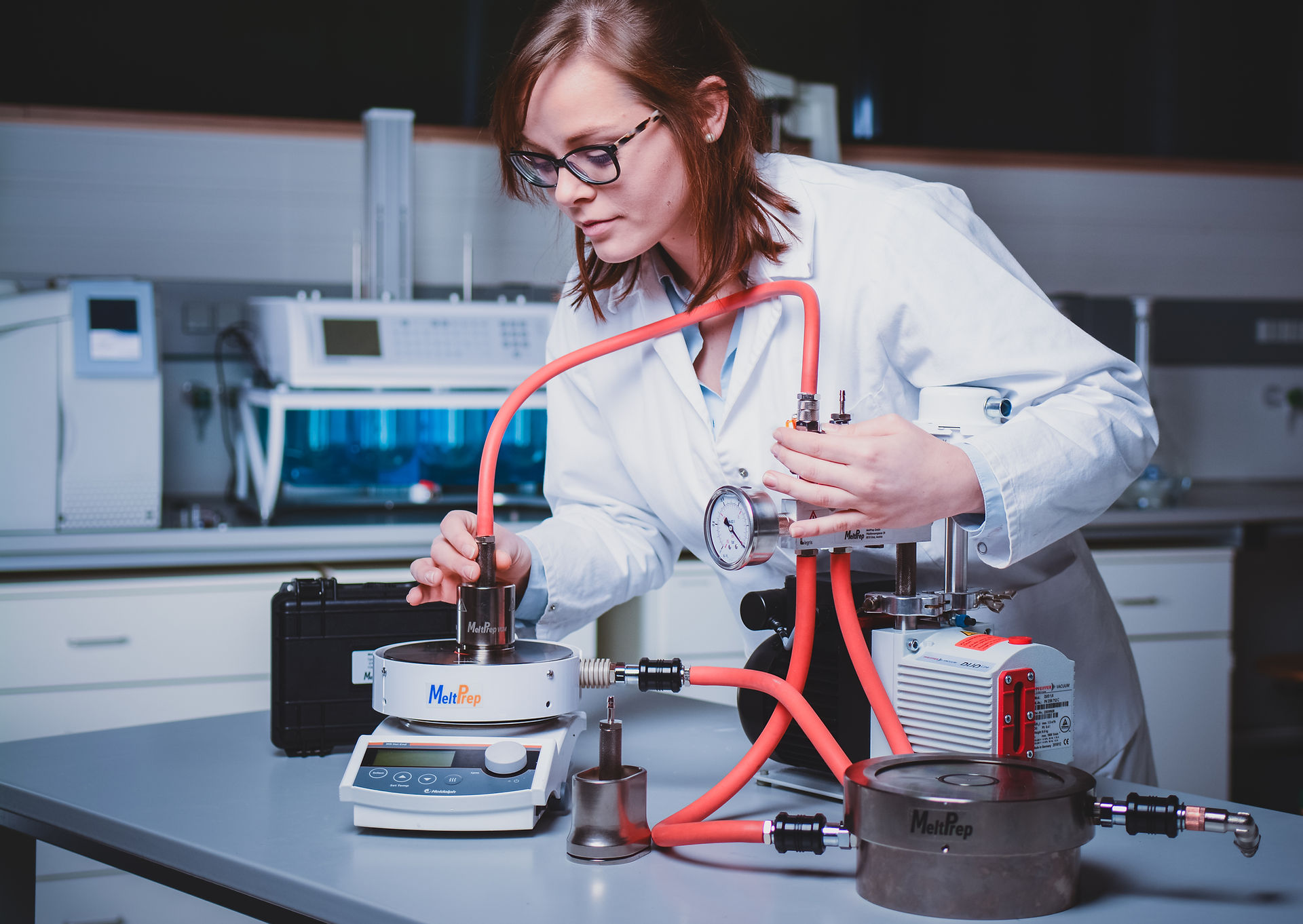
Catalyzing Innovation with Prototypes
Prototyping plays a pivotal role in advancing new developments, particularly for novel dosage forms using rare and costly materials, where batch sizes below one gram are crucial. While 3D printing offers a swift and efficient solution for engineering materials, challenges arise when altering material compositions, requiring meticulous testing and reprogramming. Free-D Molding combines the benefits of 3D printing's geometric versatility with VCM's ability to produce consistently flawless samples, enhancing the viability of manufacturing processes.

From Idea to Prototype in Hours with Free-D Molding
The Free-D Molding process starts with your concept. Share your prototype specifications with us, and we'll bring your envisioned geometry to life by 3D printing it with engineering materials. After printing the prototype, we create an in-house negative that seamlessly fits one of our VCM inserts, enabling you to use the VCM Tool with minimal material quantities for rapid prototype generation and material experimentation in your desired geometry.


It Starts With Your Idea
Free your ideas from the dusty drawers and unleash your creativity to create new dosage forms. Simply share your concept with us, and we'll craft the necessary components to bring it to life.

3D Printing With Engineering Material
We produce a 3D-printed prototype of your preferred geometry through a standardized process utilizing high-quality engineering materials.

In-House Custom Molding
A negative of the 3D-printed prototype is produced in-house, creating a Free-D mold to seamlessly fit into our VCM inserts.

VCM Process With Minimal Material
Leverage VCM to generate individual prototypes with only grams of material and rapidly experiment with various materials effortlessly.

Initiate Your Research Journey
Quickly producible and replicable prototypes can be immediately utilized in your research, accelerating your development process.
Free-D Molding Custom Geometries
Shape Your Ideas and Challenge Us with New Geometries!
We've successfully crafted a diverse array of geometries designed for a range of applications - from subcutaneous dosage forms utilizing various oral tablet shapes to intricate inner-ear implants.
Depending on the mold setting, we can alter the surface contour on one side while maintaining the base layer (imprint Free-D Molding) or use a split mold (Split Cavity Free-D Molding) for true 3D molding. The material melts in the VCM chamber and flows through the sprue into the cavity to form a new 3D part.

Imprint Free-D Molding
Creating microneedle patches is simple with imprint Free-D Molding. With the technology of VCM, you can prototype microneedle patches and more in just minutes. Simply place the desired Free-D Mold on your material within the VCM chamber; as the material melts, it adopts the shape of the mold. Whether you need single imprint or multi-rod molds, Free-D has all your research needs to be covered.


Split-Cavity Free-D Molding
Split-cavity molding offers flexibility in designing complex geometries. This process involves a mold with a top and bottom mold part, where the material placed underneath within the VCM chamber is pushed up through the sprue under vacuum compression during heating. Free-D Molding offers split-cavity molds for a wide range of applications, including bone screws, tablet shapes, rings, and tubes.

Multi-Cavity Free-D Molding
Free-D Molding also employs advanced multi-cavity molding as a cutting-edge prototyping method for developing polymer components, implants, or tablets, with the goal of improving efficiency and output during the prototyping phase. Unlike traditional single-cavity molds, Free-D's multi-cavity molding technique allows the simultaneous creation of numerous identical prototype parts in a single cycle. This not only boosts productivity but also reduces per-unit prototyping costs by leveraging economies of scale. By utilizing molds with multiple cavities, Free-D enables the swift and precise production of intricate and complex prototypes.
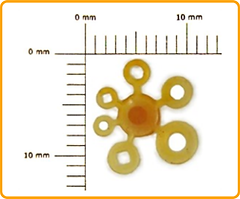
Free-D Molding Multi-material Formulations
Free-D Molding allows for multi-material formulations in either a core-sheath structure or as a multiple unit pellet system (MUPS). This process involves several steps: each formulation undergoes its own VCM cycle, and then they are fused together in an additional VCM cycle. The number of VCM cycles needed depends on the number of formulation layers in the prototype.
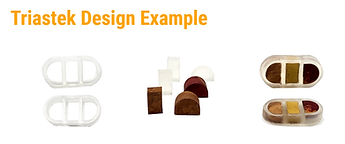

Free-D's cutting-edge prototyping method has applications across various industries.
Have an innovative idea? Contact our experts to bring your vision to life with a custom Free-D mold!